Tools 1
Coatings & Industry > CORROSION > Specimen preparation
The correct and precise specimen preparation is
very important to get repeatable results.
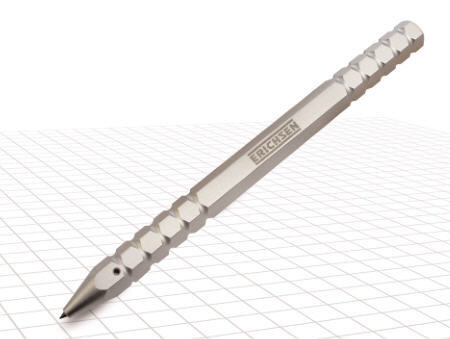
Scratching Tool acc. to van Laar, Model 426
Purpose and Application
Scratching-in of the St. Andrew's cross into test panels is a well-known preparation for short-term and endurance corrosion tests, enabling the examination of the protection of the coating against rusting of the substrate underneath the coating ("underrusting").
The Sratching Tool acc. to van Laar is a handy universal tool: for producing accurately defined incisions on the surface of the coating in preparation of forced corrosion tests, such as salt spray, continuous or intermittent immersion, accelerated weathering, gas corrosion and humiditiy tests.
Design of Apparatus
The 0.5 mm dia. spherical tungsten scratch needle is firmly mounted in a pencil-shaped holder made of anodized hard aluminium.
The special handy design of the instrument guaranties a stable appliance during the scratching operation.
The spherical point was submitted to the following endurance test:
A cylinder of 100 mm dia. free-cutting steel chucked in a lathe was scratched by a scratch needle at a surface speed of 20 cm/s (8") and a pressure of 50 N .
No damage of the spherical point did occur after a run of 18000 cm .
It proved that at least 2000 scratches of 90 mm length each can be made without a failure.
Principle of the Test
For producing a specified incision in the protective coating, the test panels are scratched with the scratching needle at the beginning of the corrosion test and again at regular time intervals.
These scratches are made horizontally, one above the other, the first at the bottom on the shorter side of the panel.
By this method it is easy to study the progression of the "underrusting".
More or less strain will have to be exerted according to the thickness and hardness of the coating in order to reach the substrate with certainty and to produce a slight deformation of the metal.
For drawing a clean scratch should be about 10 cm/s.
Evaluation of the Test
As spreading rate the number of days is recorded it takes to form 1 mm of "underrusting".
The extent of the rusting is measured from the edge of the original scratch track.
If good adhesion prevails, the track width in the metal is about 0.5 mm, with bad adhesion, however, part of the coating chips off at the edges.
(The mean width of the chipped-off film can be taken as a measure for the adhesive strength of the film and for its change in the course of the test.)
In every case, it is the "underrusting" i.e. the rust below the adhering coating formed after scratching that is to be measured.
The adjoining sketch demonstrates a case at which the paint coat was slightly chipped next to the scratch track.
The full extent of the spreading rust is essentially measured in both directions, the bare part is then deducted and the result divided by 2 in order to obtain the mean extent of the "underrusting".
For good adhesion is the "underrusting" index r therefore:
C-0,5
R= ------
2
when c = is the over-all width of the "underrusting" in mm.
Further useful suggestions as to the evaluation of corrosion tests can be found in the paper by van Laar mentioned below.
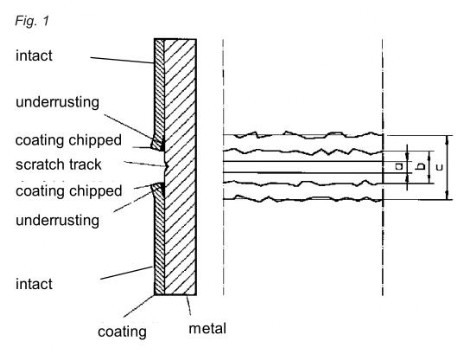
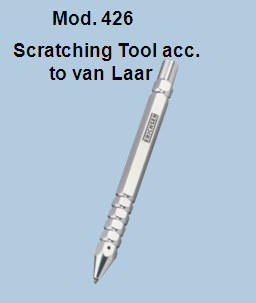
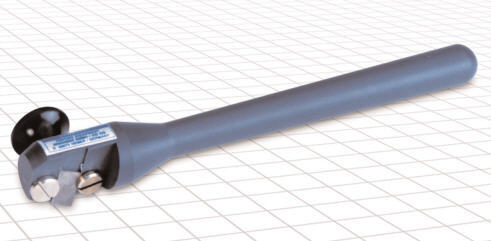
Scratch Stylus acc. to Sikkens, Model 463
Application and Test Principle
The scratching stylus method is used to produce defined damages (cracks) on coated test panels to be used in corrosion tests, as, for instance, the Fog Spray Test acc. to DIN EN ISO 9227 with the ERICHSEN Corrosion Testing Apparatus, Models 606 and 608.
This method provides a criterion for the evaluation of the extent or influence of corrosion underneath a coating and its effect on the adhesion. The length of the lateral damage underneath the coating serves as a measure of the corrosion protection factor.
Design and Function
The Scratch Stylus acc. to Sikkens, Model 463, consists of a carbide cutting blade guided by a supporting knob and a grip.
In the standard version of Model 463 the cutting blade has a width of 1 mm and rectangular edges-right angled edges.
It is adjustable in the horizontal direction by raising or lowering the cutting blade, using the locking screws.
Upon request, a carbide cutting blade of 0.5 mm can also be supplied.
Execution of the Test
Turn the adjustment screws to align the cutting edge so that it is in line with the support head.
The test panels are prepared with one or several straight scratch tracks over the whole of the metal sheet width in such a manner that they lie parallel to the narrow edge of the sheet and penetrate to the substrate.
In some cases a St. Andrew's Cross scratch track may be necessary.
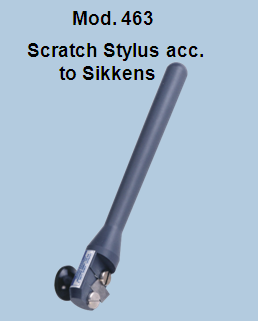
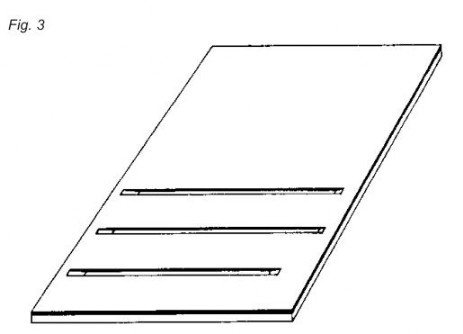
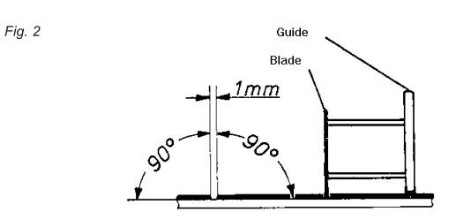
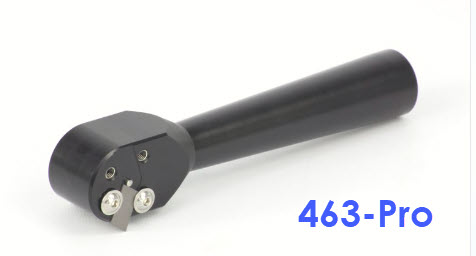
Sample Preparation Model 463-Pro
The Sikkens model 463 Pro scratch stylus
Hand-held tool for applying defined damages (scribes) on coated test panels; universally handy handle, guide wheel and a Sikkens cutting edge of 1.0 mm (both sides usable)
The Scratch Stylus acc. to Sikkens, Model 463-Pro, consists of a carbide cutting edge guided by a supporting knob and a grip.
In the standard version of Model 463-Pro the Sikkens cutting edge has a width of 1.0 mm and rectangular edges.
It is adjustable in the horizontal direction by raising or lowering the cutting edge, using the locking screws.
Upon request, Sikkens cutting edges of 0.5 mm and 2.0 mm can also be supplied; the cutting edges can be used on both sides
The Scratch Stylus acc. to Sikkens, Model 463-Pro is used to produce defined damages (scribes) on coated test panels to be used in corrosion tests, as, for instance, the Fog Spray Test acc. to DIN EN ISO 9227 with the ERICHSEN Corrosion Testing Apparatus, Models 606 and 608.
This method provides a criterion for the evaluation of the extent or influence of corrosion underneath a coating and its effect on the adhesion.
The length of the lateral damage underneath the coating serves as a measure of the corrosion protection factor.
Design and Function
The Scratch Stylus acc. to Sikkens, Model 463-Pro, consists of a carbide cutting edge guided by a supporting knob and a grip. In the standard version of Model 463 / 463-Pro the Sikkens cutting edge has a width of 1.0 mm and rectangular edges.
It is adjustable in the horizontal direction by raising or lowering the cutting edge, using the locking screws.
Upon request, Sikkens cutting edges of 0.5 mm and 2.0 mm can also be supplied; the cutting edges can be used on both sides.
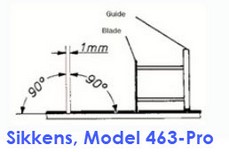
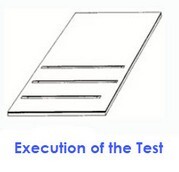
Execution of the Test
The test panels are prepared with one or several straight scratch tracks over the whole of the metal sheet width in such a manner that they lie parallel to the narrow edge of the sheet and penetrate to the substrate.
In some cases a St. Andrew's Cross scratch track may be necessary.
Scope of delivery
- Ref. 10132830131
- Scratch Stylus acc. to Sikkens, Model 463-Pro
- Sikkens cutting edge 1.0 mm
Accessories
- Ref. 101910926442 Sikkens cutting egde 0.5 mm (both sides usable)
- Ref. 101910926441 Sikkens cutting edge 1.0 mm (both sides usable)
- Ref. 101910926443 Sikkens cutting egde 2.0 mm (both sides usable)
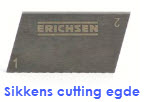
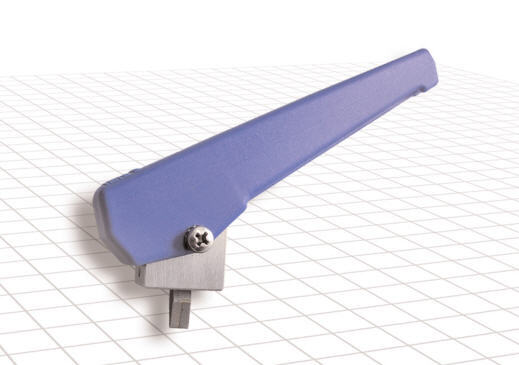
Scratching Tool acc. to Clemen, HANDCUTTER 428
Purpose and Application
It is a common method to prepare coated test panels for corrosion tests by applying various linear scratches in a vertical, horizontal or intersecting manner in such a way that the resistance of the coating system against rust formation under the coating can be tested.
Beside the use of a test tip according to "van Laar" as scratch tool, frequently the use of a test tip according to "Clemen" (included in the scope of supply) is specified for this procedure.
Sometimes a single test tip for cross hatch cutting tests may also be used.
Depending on the requirements the user has to meet, these test tips used as scratch tools are appropriate tools to produce defined scratches on coating surfaces provided for accelerated corrosion tests, such as condensation water tests, gas corrosion tests, salt spray tests, continuous or alternate immersion tests and accelerated weathering tests etc.
Design
A solid adapter block made of stainless tool steel and intended as tool holding fixture, is mounted into a sturdy plastic handle built in a highclass ergonomic manner to produce as fatigue-free as possible scratches through the often hard lacquer surfaces with the necessary force.
The scope of supply of the HANDCUTTER 428 includes the test tip in accordance with "Clemen" (R 1mm) as a scratch tool.
Optionally, the above mentioned test tips in accordance with "van Laar" (0,5 mm) or for cross hatch cutting tests (30°), respectively, can be used.
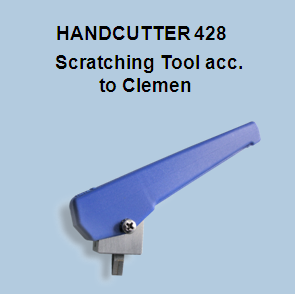